Introduction to Grass Pellet Mills
Grass pellet mills are specialized machines engineered to compress grasses into dense, homogeneous pellets. These versatile devices are crucial in various industries due to their efficiency in converting raw grass materials into a more manageable and utilitarian form. The primary function of a grass pellet mill is to process different types of grasses, including but not limited to, alfalfa, fescue, and switchgrass, into pellets. These grass pellets serve a myriad of purposes, making the grass pellet mill a valuable asset in both agricultural and industrial sectors.
One of the most common applications of grass pellets is in the realm of animal husbandry. As a nutritious and sustainable feed option, grass pellets offer a balanced diet to livestock, aiding in their overall health and productivity. Furthermore, the uniform size and composition of these pellets ensure ease of storage and transport, while also minimizing feed wastage.
Apart from their utility in animal nutrition, grass pellets have garnered attention as a renewable energy source. The process of using grass pellets as biofuel is gaining traction, especially in regions aiming to reduce their reliance on fossil fuels. When used in pellet stoves or boilers, these grass-derived pellets produce a significant amount of heat energy, contributing to a more eco-friendly and sustainable energy solution.
Additionally, grass pellet mills are finding niche applications in certain industrial processes. Specific industries require grass pellets as part of their raw material feedstock, leveraging the compact nature and consistent quality of the pellets for optimized manufacturing outcomes.
The significance of grass pellet mills transcends their practical benefits; they play a crucial role in promoting environmental sustainability. By converting biomass into valuable pellets, these machines help in reducing waste, promoting recycling, and fostering a circular economy. As the demand for sustainable practices continues to grow, the adoption and implementation of grass pellet mills are poised to become increasingly mainstream.
Uses of Grass Pellet Mills
Grass pellet mills play a pivotal role in transforming raw grass into compact pellets, which serve various industrial functions. One of the primary uses of these mills is in animal feed production. Grass pellets offer significant benefits to livestock farmers, particularly due to their dense nutritional content. For cattle, sheep, and goats, grass pellets provide a steady, balanced diet that enhances overall health and productivity. The uniformity of these pellets ensures consistent intake, leading to better growth rates and improved digestive efficiency among livestock.
Another noteworthy application of grass pellet mills is their role in biofuel production. Grass pellets represent an environmentally friendly alternative to traditional fossil fuels. Their high calorific value coupled with low moisture content makes them an efficient energy source. When burned, grass pellets produce considerably lower levels of greenhouse gases compared to coal or petroleum-based fuels. This attribute is especially significant amidst the growing global emphasis on reducing carbon footprints. Biofuel, in the form of grass pellets, emerges as a sustainable energy solution, contributing to cleaner, greener energy initiatives.
Beyond animal feed and biofuels, grass pellets find niche applications in several other industries. An emerging use is in the production of bioplastics, where grass pellets serve as a sustainable raw material. Their organic composition makes them ideal for creating biodegradable plastic alternatives, addressing environmental concerns associated with traditional plastics. Additionally, grass pellets are increasingly employed as organic fertilizers. Rich in essential nutrients, these pellets enhance soil health and fertility without the detrimental impacts linked to chemical fertilizers.
The versatile functionality of grass pellet mills underscores their importance across various domains. From optimizing animal feed to fostering sustainable energy and supporting eco-friendly agriculture and manufacturing, the applications of grass pellets are expansive and continually evolving.
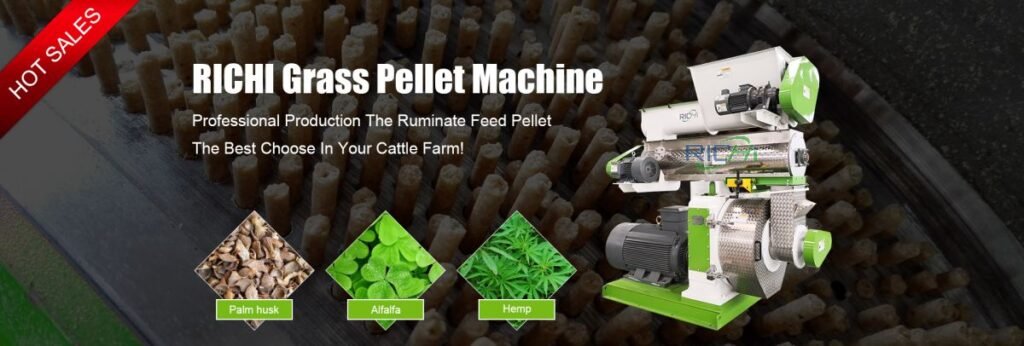
Industry Analysis and Data
The grass pellet mill industry has seen significant growth over the past few years, driven by a surge in demand for sustainable biofuels and eco-friendly agricultural practices. As the global market leans towards reducing carbon footprints, grass pellet mills have become increasingly popular. According to recent market research, the grass pellet mill market is projected to grow at a compound annual growth rate (CAGR) of 7% from 2021 to 2026. This uptick is largely attributed to rising environmental concerns and the supportive governmental policies promoting renewable energy sources.
In terms of geographic distribution, Asia-Pacific leads the market with the highest production volume, accounting for about 40% of the global share. China and India are the primary contributors within this region, where both availability of raw materials and labor cost-effectiveness play significant roles. North America and Europe follow closely, with substantial investments being made in technological advancements and efficiency improvements in grass pellet mill operations.
Market trends indicate a growing demand for advanced grass pellet mills that offer higher automation levels, leading to increased production efficiency and reduced operational costs. This has spurred the development of innovative technologies such as integrated IoT systems and AI-driven process optimizations. For instance, smart sensors and real-time analytics are being increasingly integrated into grass pellet mills to enhance their performance and maintenance schedules.
The industry’s supply chain analysis reveals a robust network encompassing raw material suppliers, equipment manufacturers, distributors, and end-users such as small-scale farmers and large energy production companies. Statistically, North America reported a production volume of approximately 2 million metric tons in 2020, with a sales revenue crossing the $500 million mark. Europe followed with an impressive 1.5 million metric tons in the same year.
Key market players like Andritz AG, CPM Holdings Inc., and Buhler Group maintain a substantial hold on the market, constantly innovating to align with the dynamic needs of the industry. Emerging technologies such as nano-material enhancements and high-efficiency biomass converters are poised to further revolutionize the grass pellet mill industry, ensuring a promising future for this environmentally vital sector.
Classification and Working Principle of Grass Pellet Mills
Grass pellet mills can primarily be classified into two types: flat die pellet mills and ring die pellet mills. Each design has its unique features and specific applications, offering particular advantages depending on the operational requirements and scale of production.
Flat die pellet mills are predominantly used for small to medium-scale productions. This type of grass pellet mill operates using a flat die and a set of rollers. The raw material is fed into the hopper, where it falls onto the flat die. As the rollers rotate, they press the grass material through the holes in the die, forming pellets. The simplicity of the flat die pellet mill’s design allows for easy maintenance and low operational costs, making it a popular choice for small farms and household use.
In contrast, ring die pellet mills are more suitable for large-scale production. These mills have a cylindrical die that rotates, with internal rollers that press the raw material against the die. This method generates higher pressure and temperature, facilitating the production of high-density grass pellets. The continuous feeding mechanism in ring die pellet mills supports consistent production rates, vital for industrial applications where efficiency and output are paramount.
The working principle of both types involves the following mechanical process: raw material feeding, pressing, pelletizing, and cooling. Initially, raw grass material is fed into the hopper. In flat die mills, gravity assists this process, while in ring die mills, mechanical feeders might be used to ensure continuous feeding. The pressing stage involves compressing the material through the die holes, shaping it into elongated pellets.
After being extruded, the pellets are cut to the desired length and ejected from the die. The newly formed pellets are usually hot and soft; thus, a cooling system is essential to lower their temperature and harden them, ensuring structural integrity. Once cooled, the pellets are ready for packaging and storage.
Both flat die and ring die grass pellet mills play crucial roles in converting raw grass into uniform, durable pellets, suitable for various applications. Understanding the distinctions and working principles of these mills helps in choosing the appropriate equipment that aligns with production goals and capacity demands.
Process Flow of Grass Pellet Production
Understanding the process flow of grass pellet production is crucial for anyone looking to enter the field. The production of grass pellets involves several meticulously coordinated stages that ensure the transformation of raw material into a high-quality, market-ready product. Below, we detail the step-by-step process from raw material collection to final packaging.
The first stage begins with the collection and preparation of raw materials. Grass, whether sourced from natural meadows or cultivated farms, needs to be harvested at the optimal time to maintain high nutrient content. Depending on the type of grass and its moisture content, the harvested grass may require drying. Air drying or mechanical drying methods can lower the moisture content to the desired range, usually around 15%.
Next, the dried grass is subjected to grinding. A hammer mill or a similar device is used to break down the grass into smaller particles. This is a crucial step, as uniformity in particle size greatly affects the quality of the final pellets. Properly ground grass ensures consistent pellet formation and reduces wear and tear on the grass pellet plant machinery.
The core of the production process is pelletizing. During this stage, the ground grass particles are fed into the pellet mill. The grass is subjected to high pressure and temperature, forcing it through the die holes of the pelletizing machine. This creates densified grass pellets. The precision of the pellet mill determines the uniformity and strength of the pellets, highlighting the importance of choosing high-quality pelletizing equipment.
Following pelletization, the newly formed pellets are typically hot and may still contain excess moisture. These pellets need to be cooled to obtain structural integrity and to prevent the growth of mold. A cooling system, such as a counter-flow cooler, is employed for this purpose. Post-cooling, the pellets undergo a screening process to remove any fines or broken pellets, ensuring that only complete, high-quality pellets proceed to the next stage.
The final step in the grass pellet production process is packaging. This step includes weighing, bagging, and sometimes sealing. Automated systems are frequently used to enhance efficiency. Proper packaging not only ensures the product’s longevity and ease of transport but also maintains its market appeal. Each step in this workflow is integral to producing high-quality grass pellets, aligned with industry standards and consumer expectations.
How to Choose the Right Grass Pellet Mill
Choosing the right grass pellet mill involves careful consideration of multiple factors tailored to meet specific needs. Central to this decision-making process are criteria such as production capacity, power consumption, and cost-efficiency, as these factors greatly impact both the short-term and long-term functionality and return on investment.
The production capacity should align with your expected output. Smaller operations might suffice with mills producing a few hundred kilograms per hour, while larger, industrial-scale needs may demand units capable of generating multiple tons during the same timeframe. For instance, a small livestock farm transitioned from manual feeding to a mechanized process with a grass pellet mill producing 500 kg/h, significantly improving efficiency and reducing labor costs.
Next, consider power consumption as a determining factor. Machines with advanced energy-efficient technologies can translate into substantial savings over time. A mid-sized poultry farm opted for a pellet mill with a slightly higher initial cost but with power-saving features, ultimately reducing their operational expenses by 15% annually.
Cost-efficiency encompasses both the upfront purchase price and ongoing maintenance costs. It is prudent to weigh the total cost of ownership against the prospective benefits. For example, a renewable energy company evaluated several models and selected a grass pellet mill that, despite its higher initial investment, required minimal maintenance and delivered superior pellet quality, leading to lower running costs and higher marketability of their products.
To assist potential buyers further, technical specifications and comparative tables are beneficial. For instance, a comparative chart outlining different models, their production rates, power consumption metrics, and costs can illuminate the best fit for varied requirements. Companies such as PelletTech and GreenPellet often provide detailed documentation and customer testimonials, enabling a more comprehensive assessment.
In conclusion, the right grass pellet mill should meet specific capacity needs, ensure energy efficiency, and offer cost-effective operation. Thorough research and real-world case studies can substantially aid in making an informed decision, paving the way for optimum performance and growth.
Choosing a Grass Pellet Mill Supplier
Identifying a dependable grass pellet mill supplier is a critical step toward ensuring efficient and long-lasting pellet production. The first characteristic to scrutinize in a supplier is their capability to customize pellet production lines. A robust supplier should provide tailored solutions that accommodate unique production needs, encompassing everything from small-scale setups to full-scale industrial operations.
Additionally, a comprehensive service offering is paramount. This includes not just the supply of machinery but also ancillary services such as installation, maintenance, and operator training. Suppliers that focus on the entire lifecycle of the pellet mill, offering turnkey projects that start from site design and extend to after-sales support, exhibit a higher level of commitment to customer satisfaction.
Richi Machinery Company exemplifies these qualities. Known as the largest pellet production line manufacturer in Henan, China, Richi Machinery excels in delivering customized solutions that meet specific client requirements. Their extensive portfolio spans across various services including meticulous site design, efficient installation processes, and ongoing operational support. This holistic approach ensures that each grass pellet mill is optimized for performance and reliability.
Moreover, Richi Machinery’s expertise in turnkey projects provides a significant advantage to their clients. Turnkey projects involve a comprehensive approach where the supplier manages every phase of the project, from initial concept and planning to the final build and operational handover. This seamless integration minimizes downtime and operational disruptions, enabling a smoother transition to full-scale production.
Evaluating potential suppliers on these benchmarks will facilitate the selection of a partner who not only delivers high-quality equipment but also supports the continuous success of your pellet production endeavors. By opting for a supplier like Richi Machinery, companies can achieve a durable and efficient grass pellet production line tailored to their specific requirements.
Practical Application Value and FAQs
The practical application value of grass pellet mills is extensive, particularly for agricultural operations and renewable energy initiatives. A grass pellet mill transforms grass and other biomass materials into compact pellets that can be used as organic fertilizer, livestock feed, or biofuel. These pellets are easy to store, transport, and handle, making them a versatile solution for various uses.
One of the primary benefits of using a grass pellet mill is the ability to convert low-value biomass into a valuable commodity. For farmers, this process not only maximizes the utility of residual crop materials but also reduces waste. The resultant grass pellets serve as high-quality fodder rich in essential nutrients, catering to the dietary needs of livestock and contributing to better animal health and productivity.
From an environmental standpoint, grass pellet mills facilitate the creation of renewable energy sources. Grass pellets, when used as biofuel, offer a sustainable alternative to fossil fuels, reducing greenhouse gas emissions and dependence on non-renewable resources. This makes grass pellet mills a critical component in the pursuit of eco-friendly energy solutions.
FAQs
What is the best way to maintain a grass pellet mill? Routine maintenance is essential for the optimal functioning of a grass pellet mill. Regularly check and replace worn parts, lubricate moving components, and ensure that the machine is free of blockages. Following the manufacturer’s maintenance schedule will help prolong the equipment’s lifespan.
How can I troubleshoot common issues with grass pellet mills? Common issues with grass pellet mills include jamming and irregular pellet size. To troubleshoot jamming, ensure that the input material is properly shredded and moisture levels are adequate. Irregular pellet size can often be corrected by adjusting the compression ratio or replacing the die and rollers.
Are there any operational tips for using a grass pellet mill efficiently? For efficient operation, ensure that the input biomass is consistently fed and that its moisture content is ideal, typically ranging between 10-20%. Pre-treating the biomass by drying or grinding can also enhance efficiency and pellet quality.
By addressing these practical aspects and frequently asked questions, potential users can gain a comprehensive understanding of how to effectively utilize grass pellet mills, ensuring they maximize the benefits these versatile machines offer.