A 20 tons per hour (t/h) poultry feed manufacturing plant represents a significant investment in the animal feed industry, designed to produce high-quality feed efficiently and consistently. Understanding the annual production capacity of such a plant is essential for effective planning, budgeting, and optimization of operations. This article explores the factors that influence the annual production capacity of a 20t/h poultry feed manufacturing plant and provides a detailed calculation of its potential output.
Key Components of a 20t/h Poultry Feed Manufacturing Plant
A typical 20t/h poultry feed manufacturing plant consists of several essential components:
- Raw Material Handling Equipment
- Grinding Equipment
- Mixing Equipment
- Pelleting Equipment
- Cooling and Drying Equipment
- Screening and Grading Equipment
- Packaging Equipment
- Auxiliary Equipment
Each component plays a vital role in ensuring the smooth operation and high efficiency of the feed production process.
Factors Influencing Annual Production Capacity
- Operational Hours Per Day
The number of hours the plant operates each day significantly affects its annual production capacity. While some plants may run continuously (24/7), others may have limited operational hours due to labor constraints, maintenance schedules, or market demand. - Number of Working Days Per Year
The total number of working days in a year also impacts the annual production capacity. This can vary based on local labor laws, holidays, and planned maintenance shutdowns. Most plants aim to maximize production by operating as many days as possible throughout the year. - Maintenance and Downtime
Regular maintenance is crucial for ensuring equipment longevity and efficiency. However, maintenance activities can reduce operational hours. Unplanned downtime due to equipment failures or other issues can also affect production capacity. - Efficiency and Automation
The level of automation and equipment efficiency can influence overall production capacity. Fully automated plants typically exhibit higher efficiency and less downtime, resulting in increased annual production. (Related post: poultry feed pellet machine price)
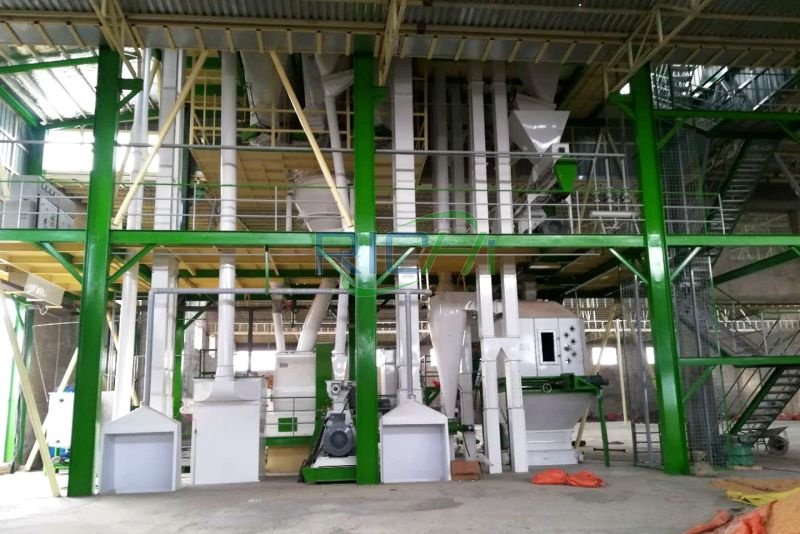
Calculating Annual Production Capacity
To calculate the annual production capacity and potential output of a 20t/h poultry feed manufacturing plant, we need to consider the following factors:
- Hourly Production Rate: 20 tons per hour
- Operational Hours Per Day: We’ll assume 20 hours per day for this calculation.
- Number of Working Days Per Year: We’ll assume 330 working days per year, accounting for maintenance and holidays.
Using these assumptions, we can calculate the annual production capacity and output as follows:
Annual Production Time (hours)Annual Production Time (hours)=Operational Hours Per Day×Number of Working Days Per Year\text{Annual Production Time (hours)} = \text{Operational Hours Per Day} \times \text{Number of Working Days Per Year}Annual Production Time (hours)=Operational Hours Per Day×Number of Working Days Per Year Annual Production Time (hours)=20 hours/day×330 days/year=6,600 hours/year\text{Annual Production Time (hours)} = 20 \, \text{hours/day} \times 330 \, \text{days/year} = 6,600 \, \text{hours/year}Annual Production Time (hours)=20hours/day×330days/year=6,600hours/year
Next, we calculate the annual production output:
Annual Production Output (tons)Annual Production Output (tons)=Hourly Production Rate×Annual Production Time (hours)\text{Annual Production Output (tons)} = \text{Hourly Production Rate} \times \text{Annual Production Time (hours)}Annual Production Output (tons)=Hourly Production Rate×Annual Production Time (hours) Annual Production Output (tons)=20 tons/hour×6,600 hours/year=132,000 tons/year\text{Annual Production Output (tons)} = 20 \, \text{tons/hour} \times 6,600 \, \text{hours/year} = 132,000 \, \text{tons/year}Annual Production Output (tons)=20tons/hour×6,600hours/year=132,000tons/year
Impact of Maintenance and Downtime
It is essential to account for maintenance and unplanned downtime when calculating the actual annual production capacity and output. Let’s assume that maintenance and unplanned downtime account for 5% of the total operational time:
Effective Operational Time (hours)Effective Operational Time (hours)=Annual Production Time (hours)×(1−Downtime Percentage)\text{Effective Operational Time (hours)} = \text{Annual Production Time (hours)} \times (1 – \text{Downtime Percentage})Effective Operational Time (hours)=Annual Production Time (hours)×(1−Downtime Percentage) Effective Operational Time (hours)=6,600 hours/year×(1−0.05)=6,270 hours/year\text{Effective Operational Time (hours)} = 6,600 \, \text{hours/year} \times (1 – 0.05) = 6,270 \, \text{hours/year}Effective Operational Time (hours)=6,600hours/year×(1−0.05)=6,270hours/year
Using the effective operational time, we can recalculate the annual production output:
Effective Annual Production Output (tons)Effective Annual Production Output (tons)=Hourly Production Rate×Effective Operational Time (hours)\text{Effective Annual Production Output (tons)} = \text{Hourly Production Rate} \times \text{Effective Operational Time (hours)}Effective Annual Production Output (tons)=Hourly Production Rate×Effective Operational Time (hours) Effective Annual Production Output (tons)=20 tons/hour×6,270 hours/year=125,400 tons/year\text{Effective Annual Production Output (tons)} = 20 \, \text{tons/hour} \times 6,270 \, \text{hours/year} = 125,400 \, \text{tons/year}Effective Annual Production Output (tons)=20tons/hour×6,270hours/year=125,400tons/year
Factors to Optimize Annual Production Capacity
- Regular Maintenance Schedules
Implementing a proactive maintenance schedule can minimize unplanned downtime and ensure that equipment operates efficiently. Regular maintenance can help identify and address potential issues before they lead to significant disruptions. - Advanced Automation
Investing in advanced automation systems can enhance efficiency and reduce the need for manual intervention. Automated systems can monitor and adjust production parameters in real-time, leading to more consistent output and reduced downtime. - Efficient Raw Material Handling
Ensuring a steady and efficient supply of raw materials can prevent production bottlenecks. Automated raw material handling systems can streamline the process and reduce the risk of delays. - Skilled Workforce
Training and retaining a skilled workforce can improve overall plant efficiency. Skilled operators can quickly address issues and optimize production processes, contributing to higher annual production output. - Energy Management
Efficient energy management can reduce operational costs and improve production efficiency. Implementing energy-saving technologies and practices can contribute to a more sustainable and cost-effective production process.
Conclusion
The annual production capacity of a 20t/h poultry feed manufacturing plant is influenced by several factors, including operational hours, the number of working days, maintenance schedules, and equipment efficiency. Based on typical assumptions, a fully automated plant operating 20 hours per day for 330 days per year can achieve an annual production output of approximately 132,000 tons. However, when accounting for maintenance and downtime, the effective annual production output is likely to be around 125,400 tons.
By optimizing factors such as maintenance schedules, automation, raw material handling, workforce training, and energy management, feed manufacturers can maximize the annual production capacity and output of the plant. By carefully considering these elements, manufacturers can ensure efficient and consistent production, meeting the growing demand for high-quality poultry feed in the market.
For details please contact: pellet machine for sale
WhatsApp:86 138 3838 9622
Email:enquiry@richipelletmachine.com