The animal feed industry is vital to agriculture, supplying essential nutrition to livestock and poultry. With the growing demand for high-quality animal feed, the efficiency of manufacturing processes is becoming increasingly crucial. Small feed factory machines, especially those with production capacities of about 3-4 tons per hour, are commonly utilized in this sector. Understanding how the production efficiency of these machines impacts overall costs is essential for feed manufacturers aiming to optimize operations and boost profitability. This article examines the connection between production efficiency and total costs in small feed factories.
1. Defining Production Efficiency
Production efficiency refers to how effectively a feed manufacturing machine converts raw materials into finished products while minimizing waste and maximizing output. Several factors contribute to production efficiency in small feed factory machines:
- Operational Speed: The speed at which a machine operates directly affects the volume of feed produced over time. Generally, higher operational speeds result in increased output, which can lower the cost per ton of feed produced.
- Energy Consumption: Efficient machines consume less energy while maintaining high production rates. Given that energy costs represent a significant portion of total production costs, machines with high efficiency can yield considerable savings.
- Material Utilization: The capacity of the machine to process raw materials effectively without excessive waste is crucial. High material utilization means more input materials are converted into finished feed, thereby reducing overall costs.
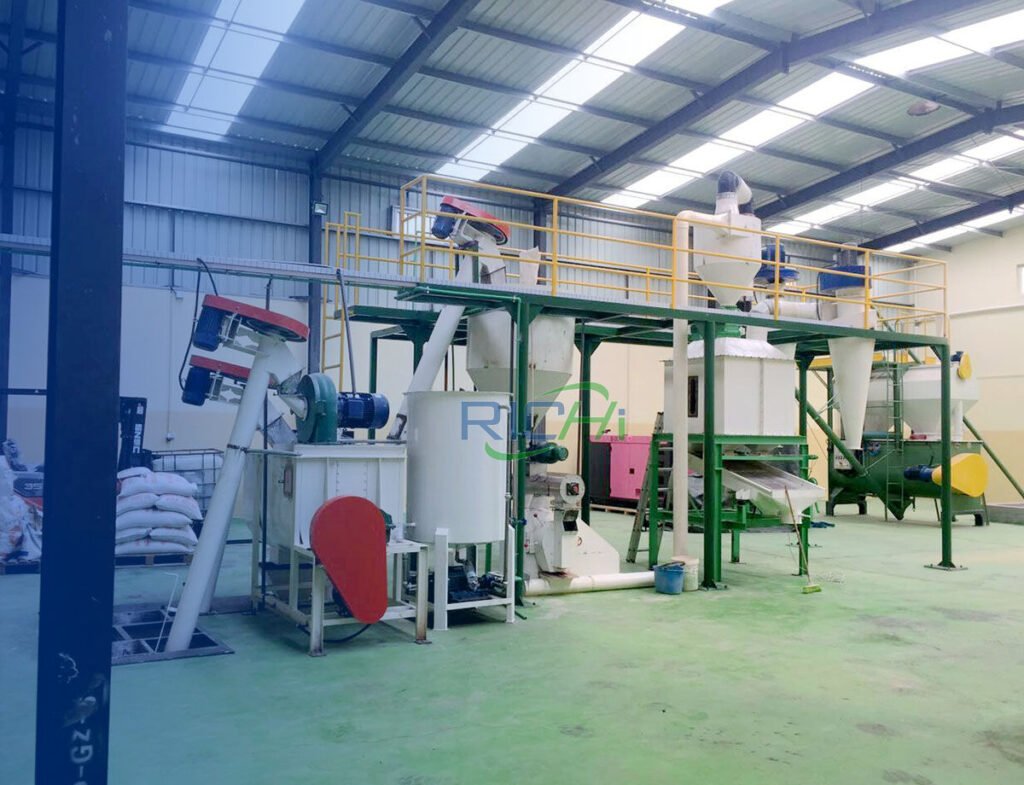
2. Effect on Direct Costs
The production efficiency of small animal feed production machine has a direct impact on various costs related to feed manufacturing.
- Raw Material Costs: Efficient machines maximize the conversion of raw materials into finished products, resulting in less waste. By minimizing waste, manufacturers can reduce their raw material costs, producing more feed from the same quantity of inputs.
- Energy Costs: Energy consumption is one of the most significant expenses in feed production. Machines that operate efficiently can drastically lower energy costs. For example, if a machine consumes 30% less energy than a less efficient model, the savings over time can be substantial, directly affecting total production costs.
- Labor Costs: Production efficiency also influences labor costs. Machines that require less manual intervention or feature automation can decrease the number of workers needed on the production line, leading to reduced labor costs and contributing to overall savings.
3. Impact on Indirect Costs
In addition to direct costs, production efficiency can also affect various indirect costs associated with operating a small feed factory.
- Maintenance Costs: Efficient machines typically incur lower maintenance costs. Smooth and consistent operation minimizes wear and tear on components, leading to fewer breakdowns and repairs. This reduction in maintenance needs can significantly decrease indirect costs over time.
- Downtime Costs: The efficiency of production directly influences the amount of downtime experienced by the machine. Inefficient machines may require more frequent repairs or adjustments, leading to increased downtime. Each hour of downtime results in lost production and revenue, emphasizing the importance of investing in efficient machines.
- Quality Control Costs: Higher production efficiency often correlates with improved product quality. Efficient machines produce consistent feed pellets with fewer defects, reducing the need for rework or extensive quality control measures, ultimately leading to lower costs associated with quality assurance and customer complaints.
4. Long-Term Financial Considerations
Investing in small feed factory machines that offer high production efficiency can have significant long-term financial implications for feed manufacturers.
- Return on Investment (ROI): Efficient machines can provide a faster return on investment. Lower operational costs, combined with increased output, can enhance profitability. Manufacturers can recover their initial investment more quickly when production efficiency is prioritized.
- Scalability: Efficient machines facilitate easier scalability. As demand for animal feed rises, manufacturers can increase production without needing additional equipment. This flexibility enhances market competitiveness and profitability.
- Sustainability: In today’s market, sustainability is increasingly important. Efficient machines that reduce waste and energy consumption contribute to more sustainable production practices, enhancing a company’s reputation and appealing to environmentally conscious consumers.
5. Conclusion
The production efficiency of small feed factory machines significantly influences total costs in animal feed manufacturing. By maximizing operational speed, minimizing energy consumption, and ensuring effective material utilization, manufacturers can lower direct costs associated with raw materials, energy, and labor. Additionally, improved efficiency can reduce indirect costs related to maintenance, downtime, and quality control.
Investing in high-efficiency feed manufacturing equipment is crucial for feed producers seeking to enhance profitability and sustainability. As the demand for high-quality animal feed continues to grow, prioritizing production efficiency will be essential for success in this competitive industry. By understanding the relationship between production efficiency and total costs, manufacturers can make informed decisions that contribute to their long-term success and growth in the animal feed market.
For details please contact: pellet mill for sale
WhatsApp:86 138 3838 9622
Email:enquiry@richipelletmachine.com