Hay is a vital component of goat diets, offering essential fiber and nutrients. Converting hay into pellets using a Goat Feed Pellet Making Machine can improve storage, reduce waste, and enhance feed palatability. This guide outlines the specific steps involved in processing hay into pellets, ensuring high-quality feed for goats.
Step 1: Hay Selection and Preparation
Choose High-Quality Hay:
- Select hay free of mold, dust, and foreign materials.
- Opt for hay with a high leaf-to-stem ratio to maximize nutritional value.
Assess Moisture Content:
- Aim for hay with a moisture content of 10-15%.
- If necessary, dry the hay to reach the optimal moisture level.
Reduce Hay Size:
- Use a hay chopper or grinder to cut the hay into uniform pieces.
- Target a particle size of 3-6 mm for efficient pelleting.
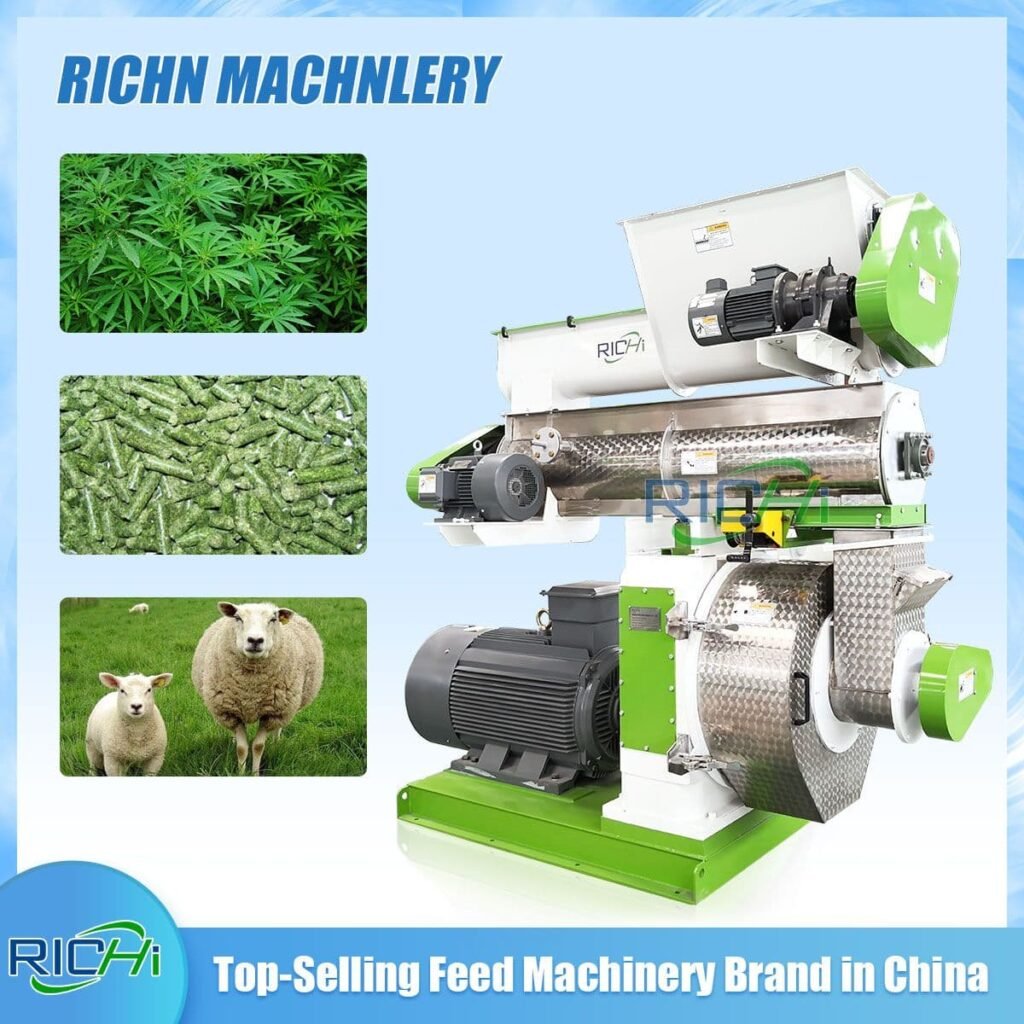
Step 2: Mixing and Formulation
Formulate the Feed Mix:
- Determine the appropriate ratio of hay to other ingredients, if any.
- Consider adding binders or nutritional supplements to enhance pellet quality.
Mix the Ingredients:
- Use a horizontal mixer to blend the chopped hay with other components.
- Ensure thorough mixing for a consistent feed composition.
Step 3: Conditioning
Pre-Condition the Mix:
- Transfer the mixture to the pellet machine’s conditioner.
- Add steam or hot water to adjust moisture content to 15-18%.
- Maintain a temperature between 60-80°C (140-176°F) for optimal conditioning.
Retention Time:
- Allow the mix to remain in the conditioner for 30-60 seconds.
- This step softens the hay fibers and activates natural binding agents.
Step 4: Pelleting Process
Feed the Conditioned Mix:
- Transfer the conditioned hay mix to the pellet mill’s feeder.
- Maintain a consistent feed rate for uniform pellet production.
Compression and Extrusion:
- The mixture is pressed through the die holes under high pressure.
- Rollers compress the material, forming pellets as it passes through the die.
- Friction-generated heat further cooks and solidifies the pellets.
Die Selection:
- Use a die with 4-6 mm holes, suitable for goat feed pellets.
- Adjust the die hole size and thickness according to the hay’s characteristics.
Parameter Adjustments:
- Monitor and fine-tune the roller-die gap for optimal compression.
- Control the feed rate to maintain consistent pellet quality.
Step 5: Cooling and Drying
Hot Pellet Discharge:
- Freshly extruded pellets exit the die at temperatures of 80-90°C.
- Immediately transfer the hot pellets to a cooling system.
Cooling Process:
- Use a counter-flow cooler to reduce pellet temperature.
- Cool the pellets to within 5°C of ambient temperature in about 5-10 minutes.
Moisture Reduction:
- Ensure the pellet moisture content decreases to 10-12% during cooling.
- Proper cooling is crucial for pellet stability and storage longevity.
Step 6: Screening and Sorting
Screen the Pellets:
- Pass the cooled pellets through a screener to remove fines and dust.
- Separate any oversized or broken pellets.
Recycle Fines:
- Collect fines and return them to the pelleting process for reprocessing.
- This step enhances efficiency and minimizes waste.
Step 7: Quality Control
Physical Quality Checks:
- Test pellet durability with a pellet durability tester.
- Assess pellet hardness and measure density and uniformity.
Nutritional Analysis:
- Conduct regular nutrient testing to ensure the pellets meet dietary requirements.
- Monitor protein content, fiber levels, and other essential nutrients.
Moisture Content Verification:
- Confirm that the final pellets have a moisture content within the 10-12% range.
Step 8: Packaging and Storage
Packaging:
- Package pellets in appropriate bags (e.g., 25 kg or 50 kg).
- For larger operations, consider bulk packaging.
Labeling:
- Clearly label packages with product information, production date, and nutritional content.
Storage Conditions:
- Store pellets in a cool, dry place to preserve quality.
- Implement a first-in, first-out (FIFO) inventory system.
Step 9: Equipment Maintenance
Regular Cleaning:
- Clean the pellet mill, cooler, and associated equipment after each production run.
- Pay special attention to cleaning the die and rollers to prevent buildup. (Related post:livestock feed pellet machine)
Wear Part Inspection:
- Regularly inspect dies and rollers for wear and replace them as needed.
- Check other critical components for signs of damage.
Lubrication:
- Follow the manufacturer’s guidelines for lubricating moving parts.
- Maintain a regular lubrication schedule to ensure smooth operation.
Step 10: Record Keeping and Process Optimization
Production Logs:
- Keep detailed records of each production batch.
- Document machine settings, ingredient ratios, and quality control results.
Performance Analysis:
- Regularly review production data to identify areas for improvement.
- Analyze energy consumption, production rates, and pellet quality.
Continuous Improvement:
- Use collected data to optimize the pelleting process.
- Experiment with different settings and formulations to enhance efficiency and pellet quality.
Conclusion
Processing hay with a Goat Feed Pellet Making Machine involves a series of meticulous steps, from selecting and preparing hay to final packaging. Each step is crucial to producing high-quality pellets that are nutritious, palatable, and easy to store. By adhering to these guidelines and maintaining rigorous quality control, operators can ensure the production of premium hay pellets that contribute to optimal goat nutrition and farm efficiency. Continuous monitoring and process refinement are key to mastering this process and achieving consistent results.